By Kevin Parmenter, Taiwan Semiconductor
An industry expert offers advice on how to avoid buying fake components
Due to the semiconductor industry’s global supply chain issues the risk of buying counterfeit devices is high. When fake parts make it into end products, rather than being quarantined and eliminated during production, the repercussions are costly. Field failures, service calls, RMAs, loss of reputation and legal exposure – all are likely results. Buyers need to avoid buying fake parts from an unauthorized source, not through the established supply chain, and then realizing, too late, that the parts broker – and your money – is long gone.
How Did We Get Here?
A hipot tester, switch, and automated software can assure vehicle connectors are safe and reliable.
Glen Broderick , Vitrek Inc.
Loose or mismatched electrical components cause the highest rate of failures in vehicles. Often harnesses and components are inadvertently pinched, miswired or damaged during installation. Also, cable insulation that isn’t secured can wear through and cause eventual problems.
For these reasons, it is critical that automotive cable and harness assemblies be thoroughly tested and verified before installation. One proven approach to cable/harness testing combines a hipot tester, a switching system and automated software. This testing system speeds and simplifies testing in automotive applications, while also providing historical backup data to prove that components were verified prior to installation.
Vehicle harness testing verifies cable insulation for isolation, sufficiency and effectiveness. A simple insulation resistance test, also referred to the dc hipot test, employs two conductors with an insulator between them. One conductor can be a vehicle chassis, for instance, and the other a 12-V positive terminal coming off the car.
During isolation testing, high voltage is introduced to the limit desired. The test ramps voltage up from zero to 1,000 V, holds it for a specific time period, then lets it discharge. During the test, a hipot tester monitors the voltage to assure that excessive current does not flow from the conductor through the insulation to the other conductor.
BY KEVIN CLARK, VITREK INC.
Hipot testers offer a range of capabilities starting with dielectric withstand and insulation resistance testing but also, in many instances, providing accurate low-resistance measurements and low-resistance/high-current outputs to test ground resistance and ground bond integrity.
Selecting the right one for your application will ultimately save both time and expense in performing these essential tests.
Product Safety Certification Before getting into the individual functions, it is important to point out that hipot testing is a generic term.
Actual testing will require meeting different specications, depending upon where in the world the product will be sold and used. The details of what constitutes a certified product is dependent upon a daunting number (hundreds) of safety standards and the region of the world where the device
will be sold and used. Standards setting organizations include: EN / IEC (European), UL (US), CSA (Canada, Vitrek’s V7X Hipot Tester is well-suited to the requirements of electrical safety production testing.
Author: Chad Clark, VP Sales & Marketing, Vitrek, LLC
Date: 09/03/2019
The power electronics designer’s equivalent of the fabled Swiss Army Knife, the
power analyzer puts together all the tools needed....
The Swiss Army Knife (Figure 1) is a whole lot more than a knife. True, it starts out as a basic pocket knife but then it adds everything from screw-drivers, bottle opener, corkscrew, scissors and a halfdozen other useful tools.
This venerable pocket tool has been used in numerous analogies for equipment that handles a combination of functions. In that regard, it’s clear that the power analyzer is the power electronics professional’s bench-top Swiss Army Knife. Here’s why: The design of any power conversion system requires the
measurement of a large range of electrical parameters that could be made using a lab bench full of instruments. The power analyzer pulls all of these measurements into a single instrument, replacing meters, oscilloscopes, chart recorders, data loggers, harmonic analyzers and other devices.
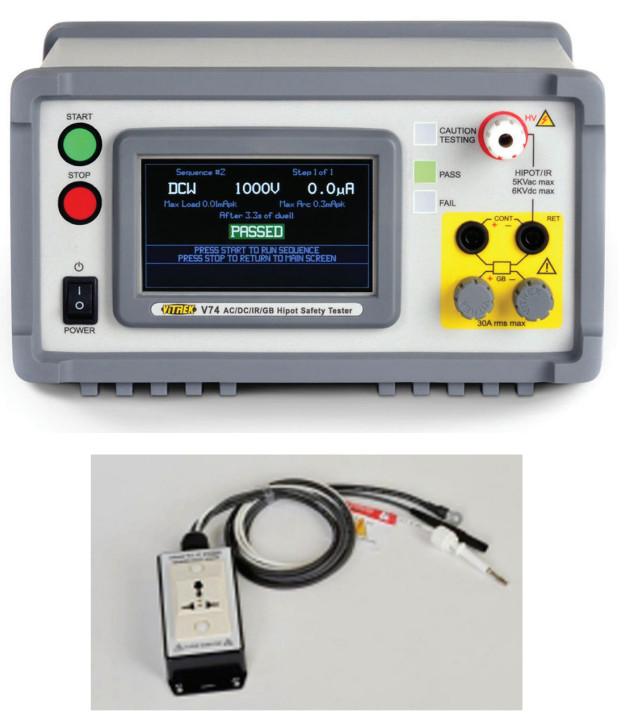
A few simple steps ensure testing takes place safely when potentially lethal voltages and currents are involved in the testing process.
KEVIN CLARK | VITREK INC.
Hipot testing has long been a standard procedure for assuring the electrical safety compliance of electronic equipment. Early commercial hipot testers were actually not much more than a variac-driven step-up transformer used to ramp up the test voltage and then dwell at the specified voltage for the prescribed time period – all the while monitoring for excessive leakage current or device breakdown. This method could easily lead to incorrect results when leakage current caused the voltage output from a high impedance transformer source to droop. Modern hipot testers utilize electronic source technology to assure compliance with IEC-61010. This standard explicitly requires that “the voltage withstand test equipment shall be able to maintain the required voltage for the specified period of time.”
There is no substitute for operator competence, so the first step to a safe testing environment is to simply provide training. The operator should be in good health; operators with special medical conditions should not work with high voltage. All operators should understand that high voltage is dangerous, and care must to taken to avoid touching energized circuits. They should have knowledge of the effects of electrical currents on the human body and how best to avoid shock hazards. It is a good idea for all employees to learn how to perform compression-only CPR.
This article provides an overview of the relevant industry standards for LED lighting products. It also describes how advanced test equipment helps ensure that LED lighting products meet all necessary parameters for performance, energy efficiency, consumption verification, and safety certification.
Standard and specification for solid-state lighting Updated in 2019 (the first time since 2008), ANSI/ IES LM-79-19 is the standard and specification for solid-state lighting. In addition to specifying optical measurements (lumens, chromaticity, luminous flux, etc.), LM-79-19 includes stringent system efficacy specifications. For LED lighting, the relevant parameters fall under “AC Power Supply Standards” (sections 5.1-5.3).
The LED driver can be integrated into the LED lighting fixture itself. In this case, the input power coming into the luminaire’s LED driver (power supply), as well as its output power, must be measured using test equipment to compute system efficiency.