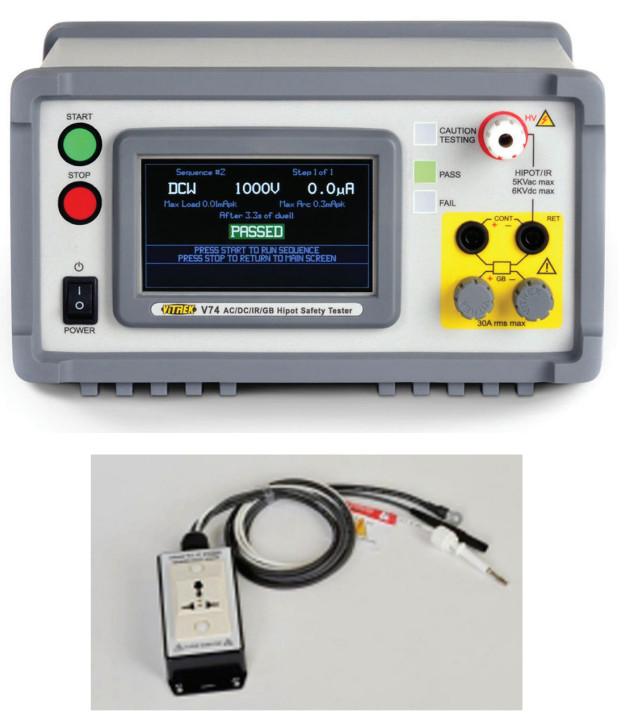
A few simple steps ensure testing takes place safely when potentially lethal voltages and currents are involved in the testing process.
KEVIN CLARK | VITREK INC.
Hipot testing has long been a standard procedure for assuring the electrical safety compliance of electronic equipment. Early commercial hipot testers were actually not much more than a variac-driven step-up transformer used to ramp up the test voltage and then dwell at the specified voltage for the prescribed time period – all the while monitoring for excessive leakage current or device breakdown. This method could easily lead to incorrect results when leakage current caused the voltage output from a high impedance transformer source to droop. Modern hipot testers utilize electronic source technology to assure compliance with IEC-61010. This standard explicitly requires that “the voltage withstand test equipment shall be able to maintain the required voltage for the specified period of time.”
There is no substitute for operator competence, so the first step to a safe testing environment is to simply provide training. The operator should be in good health; operators with special medical conditions should not work with high voltage. All operators should understand that high voltage is dangerous, and care must to taken to avoid touching energized circuits. They should have knowledge of the effects of electrical currents on the human body and how best to avoid shock hazards. It is a good idea for all employees to learn how to perform compression-only CPR.
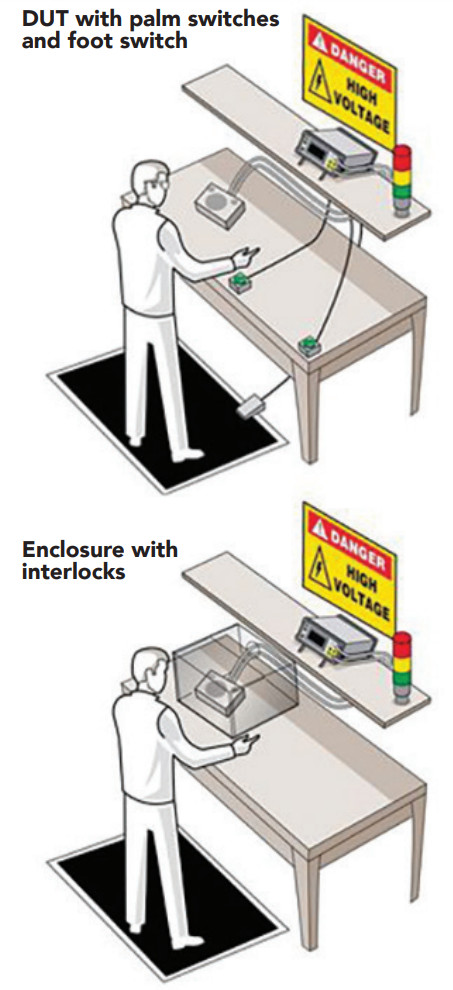
In addition, it is easy to implement circuit palm switches that prevent the operator from encountering high voltage during testing.
Operators must understand the workings and importance of safety interlocks and why the interlocks should never be disabled. They must also understand the hazards of wearing metallic jewelry around electrical equipment and show how to interrupt power quickly in emergency situations.
Other operator requirements include programming the necessary tests and storing them in memory. There should be a procedure available showing which memory location should be used for each individual device being tested. The procedure should also outline the test being performed (ac or dc, voltage, test time and limits). The operator should use the key lock feature on the tester. This will avoid programs being changed
to unknown values.
Those who train the operators should explain the object of each test, show how it should be executed, and show how to handle both normal and abnormal situations that may arise.
Make sure each operator understands how much he or she can handle alone and when supervisory personnel should be called in for help. They should hold regular meetings to review and update safety procedures and regulations.
The next step is determining where the test station will reside. The test area should be isolated from the factory assembly area. It should be away from foot traffic to assure the safety of passersby and, of course, the safety of the station operator. Operator distractions should be kept to a
minimum, and the area should be conspicuously marked with internationally approved signage, such as “DANGER – HIGH VOLTAGE.” During testing, the hipot tester itself should have indicator lights to denote when high voltage is present.
There should be ample and reliable power supplied to the test station. Verify that the power wiring meets electrical code requirements for polarization and grounding. Always use an outlet that has a properly connected protection ground and makes sure this ground has been tested to ensure a low impedance path to the panel ground and earth bonded ground. Operator injury may result if the hipot tester is not
connected to earth ground properly.
The work area and bench surface should consist of non-metallic materials; which means that metal work surfaces should be avoided, and metal objects should not be placed between the operator and DUT. All other metal objects should be grounded or be out of the test area altogether. An ESD mat is not a recommended platform for your test station, as it may cause erroneous readings for leakage and is unnecessary in this application.
In addition, the test equipment should provide for immediate and safe removal of the output voltage using internal discharge circuity at the conclusion of the test or if the test is interrupted. Never remove power for the hipot tester. If there is a power interruption, use extreme care in any contact with the DUT. The safest approach is to leave the DUT connected to the hipot tester until power is restored and the tester can conduct its discharge function.
OPERATOR SAFETY CONSIDERATIONS
The test station should have sufficient space for the tester and the DUT without the operator having to reach over the DUT to access the tester. The tester should be at least three inches away from the wall to provide proper airflow for the unit. Ideally the DUT should be isolated from the operator
and tester. For larger DUTs, which are wheeled to the test station, the cart should be non-conductive and have locking wheels. (This also applies if the tester needs to be wheeled to the DUT.) Keep the area clean and neat and arrange the equipment so that it is easy and safe for the operator to use.
There are many safety features such as guards or enclosures that can be added to the test station to prevent the operator from encountering high voltage. When placed around a DUT they should be non-conducting and carry safety interlocks that interrupt all high voltages when open. Interlocks
should be arranged so operators are never exposed to high voltages under any conditions.
In addition, it is easy to implement circuit palm switches that prevent the operator from encountering high voltage during testing. The basic operation of a palm switch requires the operator to use both hands to initiate a test with, potentially, a foot switch to activate the test. The test stops immediately if the operator removes one or both hands from the switches.
The switches are placed directly in front of the operator and spaced shoulders-width apart. Spacing the switches prevents an operator from trying to press down both buttons with one hand or object. No high voltage can be applied to the output terminals and DUT until both switches are pressed simultaneously. The operator cannot touch the DUT or test leads if both hands are on the palm switches.
The palm switches are connected to the digital I/O on the hipot tester. Putting the switches in the down position enables the start. When one switch goes up the safety interlock is enabled, terminating the output voltage of the hipot test. This method is safe, quick and effective.
There are two alternative approaches to the setup of a benchtop hipot test. In one case, the DUT is placed on the test bench and a combination of palm switches and a foot switch ensure that the operator cannot touch the DUT while the test is underway. The operator is wearing safety glasses. As a practical matter, the use of palm switches is typically restricted to shortduration tests done repetitively with a series of DUTs. If this test set up is used for longer tests, operators will find a way to defeat the palm switches.
In the second case, the DUT sits under a protective cover with an interlock to isolate the operator during the test. The use of an enclosure is a more reliable means to assuring operator safety, particularly when tests require longer time periods.
More elaborate test stations can include a hipot tester interlock. One safety method that utilizes the interlock employs a light curtain, which is an infrared light beam that will open the interlock if anyone interrupts any part of the beam. The output of the light curtain connects to the interlock terminal on the hipot tester. If the interlock opens, high voltage is immediately terminated. The light curtain is placed between the hipot tester or
the DUT and the operator. An operator touching the high voltage would have to pass through the light curtain, hence opening the interlock, which terminates the high voltage.
Of course, if the hipot sits behind the light curtain there must be a way to start the test. A foot switch is an easy solution. Keep in mind the setup must ensure nobody can reach the high voltage by going around the light curtain.
TEST SETUP
Regularly, typically at the start of every shift, the tester itself should be checked by connecting it to both PASS and FAIL samples. These samples should be designed to confirm the tester works properly for the type(s) of tests to be conducted (hipot, insulation resistance, ground resistance and ground bond).
The operator should also confirm that all test parameters, according to the test documentation, display on the tester screen.
Then the operator can run the test, keeping in mind the safety considerations this article describes.
Operator Checklist for HiPot Testing: Basic Safety Guidelines and Procedures
- Only properly trained operators should be allowed to use the equipment and have access to the test area.
- Do not make any connections to a DUT unless you have verified the high voltage warning light is OFF.
- Never touch a DUT, the tester or the test leads.
- When connecting leads to the DUT, always connect the ground clip first.
- Never touch the metal of a high voltage probe or HV test lead directly. Only touch the insulated parts and only when no high voltage is present.
- When possible, use interlocked test fixtures only.
- Verify all DUT connections before starting a test. Make sure no other objects are near the DUT or the tester.
- Keep the area neat and uncluttered and avoid crossing test leads.
- Suspend the test leads to minimize capacitive coupling.
- Follow the prescribed procedure for each test exactly as written.
- Verify all setup conditions before starting a test and examine all leads for signs of wear.
- Verify the tester is functioning properly by use of a performance verification device. This will also confirm the condition of the test leads. Keep the equipment on a regular calibration cycle.
- Have a “hot stick” handy when performing a dc test and use it to discharge any connection or device that may become disconnected during a test. This is necessary because unexpected, dangerous charges can build up during a test if a connection comes loose.
- At the completion of a test, observe that the HV light is out. If the test was dc, the discharge may take some time.
- Ensure the tester and test station uses all the built-in safety features and functions of the hipot tester.
- Periodically test the memory to ensure consistent testing and that the parameters are not altered.
- Make sure the ac mains to the tester is properly installed with low impedance ground connections. Also make sure that the emergency switch disconnects all power from the tester and the DUT and all electrical equipment and feeds in the testing area.
- Operator and nearby co-workers should be trained in compression-only CPR in the event of a heart attack event or contact with high voltage.
![]() |
|
A few simple steps ensure testing takes place safely when potentially lethal voltages and currents are involved in the testing process. |
|
![]() ![]() ![]() |
Download |