A hipot tester, switch, and automated software can assure vehicle connectors are safe and reliable.
Glen Broderick , Vitrek Inc.
Loose or mismatched electrical components cause the highest rate of failures in vehicles. Often harnesses and components are inadvertently pinched, miswired or damaged during installation. Also, cable insulation that isn’t secured can wear through and cause eventual problems.
For these reasons, it is critical that automotive cable and harness assemblies be thoroughly tested and verified before installation. One proven approach to cable/harness testing combines a hipot tester, a switching system and automated software. This testing system speeds and simplifies testing in automotive applications, while also providing historical backup data to prove that components were verified prior to installation.
Vehicle harness testing verifies cable insulation for isolation, sufficiency and effectiveness. A simple insulation resistance test, also referred to the dc hipot test, employs two conductors with an insulator between them. One conductor can be a vehicle chassis, for instance, and the other a 12-V positive terminal coming off the car.
During isolation testing, high voltage is introduced to the limit desired. The test ramps voltage up from zero to 1,000 V, holds it for a specific time period, then lets it discharge. During the test, a hipot tester monitors the voltage to assure that excessive current does not flow from the conductor through the insulation to the other conductor.
Ground testing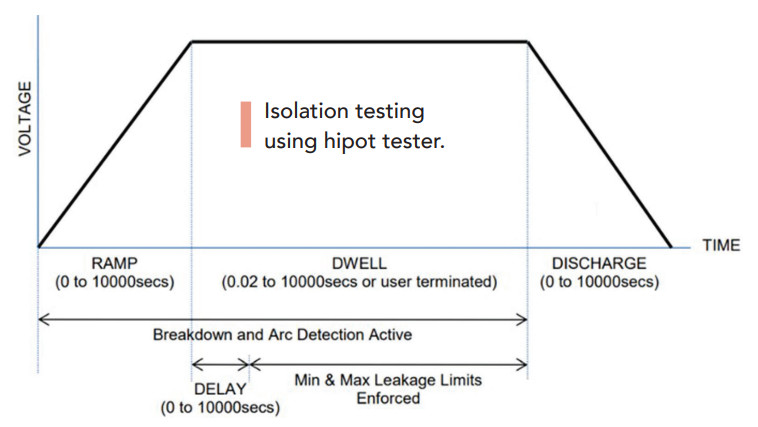
Ground testing can employ either a continuity test or a ground-bond test. Both measure continuity and the resistance to ground.
However, with ground-bond testing a high current runs through the grounding system to ensure the capacity to ground properly without melting open.
Depending on the source current (50 mA to 40 A), the user can test for:
- Type test or production
- Resistance from chassis to earth with either twowire or a four-wire Kelvin measurement
- Circuit breaker trips properly
- 100 mΩ typical limit
Typically in continuity groundbound testing, a four-wire Kelvin measurement test is used to measure low contact resistance.
During testing, the hipot sources current across the DUT, measures the voltage drop across it, and automatically converts the result into milliohms.
In contrast, for ground-bond testing, the user pushes high current through the cable. For example, the conductor may be stressed with
current levels up to 40 A, potentially generating heat. A faulty connection will cause runaway and failure.
Performed during installation, this test is key for avoiding future vehicle performance problems and, potentially, unsafe conditions.
The combined solution described here comprises three types of Vitrek test equipment: a hipot tester, a multi-point switch, and automation software. In this example, the 95X Series hipot tester performs insulation resistance, continuity and ground bond testing.
This unit is well suited for measuring lower leakage current levels in higher-voltage harness tests.
The hipot tester offers a wide range of ac/dc outputs (up to 30 kV ac and 15 kV dc) and 100 pA resolution leakage measurements.
The system can be used with or without the software because the 95X Series is capable of controlling itself and the 964i switch as a standalone system.
(With the addition of a computer and QT Enterprise software, all test data can be archived for later reference or audits.)
Also part of the combination cable/harness test system is a multi-point, multi-conductor 964i switch. The switching system offers a range of configurable voltage ratings (3,7,10 and 15 kV) with currents up to 70 A. The unit has up to eight relays per card for a total of 64 test points. Multiple chassis can be combined to increase channel count beyond 64 points.
Each 964i is custom wired per user-specific test requirements.
For instance, some people like “Y” connections where each point can be made either HV or return.
Others like one-to-one inputs and outputs that can be turned on and off individually. Still others like to have an internal HV or return bus.
Vitrek’s combination cable/harness test
solution includes a 950X Series hipot tester,
a 964i switch (below) and QT Enterprise
software (screen capture).
Any combination of points can be connected to the bus at any given time.
Integral to the combined solution, QT Enterprise software offers extremely helpful control capabilities. Used with the test equipment described above, this software enables the user to view a graphical representation of their test on a computer screen – and configure all test parameters, such as voltage and output, on easyto-read display screens.
In the event of a failure during testing, the user can set the test to stop to either re-test with a new device or continue the test process to identify any additional faults before reworking the existing device. When testing is complete, the user can save and document (and print) an unlimited number of tests on a central database for comparing and analyzing the test results of various users.
Cable manufacturers will find the software’s “global” settings especially helpful because they allow companies to personalize their testing processes. For example, a user can specify that all testing will start upon a digital I/O (DIO) input or at the click of the mouse.
When the switch is paired with a hipot tester, up to 16 chassis can be daisy-chained with hundreds of unique test points. This means the tester goes from having one high-voltage output and one return point – to having hundreds.
Typically, the user will connect one highvoltage and a return lead to run a test. The user can custom configure and display each switch according to the number and type of cards.
Unlike typical cable testers, the system allows each relay to be configured individually, which means easier testing of complicated devices.
Use of QT Enterprise software helps automate testing by giving users computercontrol of their tests. For instance, cable/harness tests can be configured according to specific performance parameters, including:
- Up to 15 kV
- Up to 70 A
- 64 relays per chassis
- Up to 16 chassis
- 100 msec/point continuity test
- 1 sec/point voltage-withstand test
- Each relay is individually controllable
- Can be ordered with configurations to connect any way each specific user requires
Example: EV charger testing
The automated harness testing system is used in an electric vehicle charging cableapplication. The equipment/software used is a Vitrek 964i high voltage switching system (and HVHC relays), a Vitrek 952i hipot tester, and Vitrek QT Enterprise software, The testing validates EV charging cables and verifies ultralow contact/cable resistance and HV insulation.
For the test, the cable sat inside a safety enclosure to ensure no high voltage was applied while the lid was open. Although the hipot testers have built-in technologies to limit discharge and quickly detect breakdown voltage, the enclosure provides additional operator safety.
Because a tremendous amount of energy goes into the system as fast as possible, the connectors must have a low contact resistance.
Meanwhile, isolation must be high, in the 5 kV range. The EV connectors, each with multiple temperature-sensing pins, etc., require at least three to five conductors each, which add to the complexity of the test.
After specifying the relay sequencing using QT Enterprise software, the application utilizes the 952i hipot tester’s high-voltage isolation test and ability to measure resistance.
The 964i switch measures contact resistance in microohms, tested at 5 kV isolation.
With 20 or more harnesses, many interfacing with digital control devices, today’s vehicles have complex electronics systems. They need precise and accurate continuity and cable testing on every connection during the assembly process to assure safety and reliability. A combination of a hipot tester, multi-point switching system and automated software shortens test time, boosts production volume and improves quality.
Automated cable testing reduces the chances of error from manual testing. It also provides manufacturers with unlimited historical data that can serve as valuable backup in case of a subsequent component failure.
References
Vitrek Inc., vitrek.com
Vitrek’s QT Enterprise software provides a
graphical representation of cable testing.
When testing cables, the user can individually
control each relay. All 64 relays connected
to the 964i switch are represented on the
screen. If there is more than one chassis,
each chassis can be selected individually and
its outputs changed. When viewing custom
configuration, the user can determine which
relays should be shut and which should
be open for each test. Here, the user has
selected boxes “1” and “33” in the blue
“Bank” columns. During testing, the user
can view the steps comprising the testing
sequence. After the test is complete, the
user can easily choose the switch setup for
the next test.
![]() |
|
![]() ![]() ![]() |
Download |